Plastic extrusion for strong and easy-to-handle components
Plastic extrusion for strong and easy-to-handle components
Blog Article
A Comprehensive Guide to the Refine and Benefits of Plastic Extrusion
In the vast realm of production, plastic extrusion emerges as a extremely effective and vital procedure. Transmuting raw plastic right into continual profiles, it satisfies a huge selection of markets with its amazing flexibility. This overview intends to illuminate the detailed actions entailed in this approach, the types of plastic proper for extrusion, and the game-changing advantages it brings to the industry. The occurring discussion assures to unravel the real-world impacts of this transformative process.
Comprehending the Basics of Plastic Extrusion
While it may appear facility in the beginning glimpse, the procedure of plastic extrusion is fundamentally basic - plastic extrusion. It is a high-volume manufacturing strategy in which raw plastic is thawed and shaped into a continuous profile. The process begins with the feeding of plastic product, in the kind of pellets, powders, or granules, into a heated barrel. The plastic is then thawed utilizing a mix of warm and shear, used by a revolving screw. When the molten plastic gets to the end of the barrel, it is compelled with a little opening recognized as a die, forming it right into a preferred type. The designed plastic is after that cooled down, solidified, and reduced right into wanted lengths, finishing the process.
The Technical Refine of Plastic Extrusion Explained
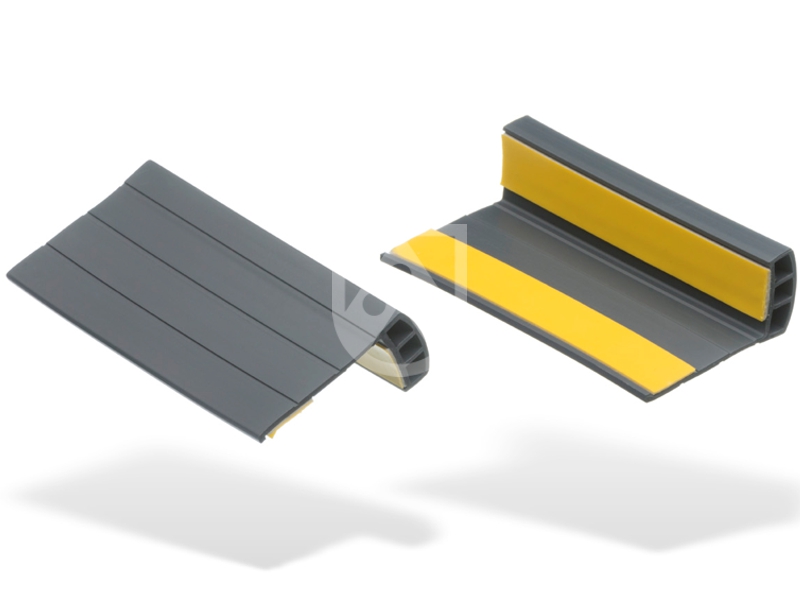
Kinds Of Plastic Suitable for Extrusion
The selection of the ideal type of plastic is an important element of the extrusion procedure. Various plastics provide one-of-a-kind homes, making them a lot more fit to certain applications. Recognizing these plastic kinds can substantially boost the extrusion procedure.
Contrasting Plastic Extrusion to Other Plastic Forming Techniques
Comprehending the kinds of plastic suitable for extrusion leads the way for a more comprehensive discussion on just how plastic extrusion compares to various other plastic developing approaches. These include injection molding, strike molding, and thermoforming. Each method has its special usages and benefits. Shot molding, for example, is exceptional for developing elaborate components, while blow molding is ideal for hollow things like bottles. Thermoforming excels at developing large or shallow components. Plastic extrusion is unequaled when it comes to producing continuous accounts, such as seals, gaskets, and pipes. It also allows for a constant cross-section along the size of the item. Thus, the option of approach mostly depends on the end-product demands and specifications.
Key Advantages of Plastic Extrusion in Production
In the world of manufacturing, plastic extrusion uses many substantial benefits. One notable advantage is the cost-effectiveness of the procedure, that makes it a financially attractive manufacturing technique. Furthermore, this strategy gives exceptional item flexibility and boosted manufacturing speed, therefore increasing general production efficiency.
Economical Production Approach
Plastic extrusion jumps to the additional hints leading edge as an economical manufacturing method in production. This process stands out for its ability to create high volumes of material swiftly and successfully, supplying producers with significant cost savings. The main cost advantage is the capability to use cheaper resources. Extrusion uses thermoplastic materials, which are less costly contrasted to metals or porcelains. Even more, the extrusion process itself is fairly basic, reducing labor costs. In addition, plastic extrusion needs less power than standard production methods, contributing to lower functional expenses. The process also reduces waste, as any type of faulty or excess products can be reused and recycled, supplying one more layer of cost-effectiveness. In general, the monetary advantages make plastic extrusion an extremely eye-catching alternative in the manufacturing sector.

Superior Product Versatility
Beyond the cost-effectiveness of plastic extrusion, another substantial benefit in making lies in its premium product versatility. This procedure permits the creation of a large array of items with differing dimensions, styles, and forms, from simple plastic sheets to elaborate accounts. The adaptability is credited to the extrusion pass away, which can be customized to generate the wanted product design. This makes plastic extrusion an optimal solution for sectors that call for customized plastic parts, such as automobile, building and construction, and packaging. The capacity to produce varied items is not only advantageous in conference specific market needs this content but likewise in making it possible for producers to explore brand-new product lines with very little capital investment. Basically, plastic extrusion's item versatility cultivates development while enhancing operational effectiveness.
Enhanced Manufacturing Speed
A considerable benefit of plastic extrusion exists in its boosted manufacturing speed. Couple of other manufacturing processes can match the speed of plastic extrusion. In addition, the capacity to keep constant high-speed manufacturing without sacrificing product quality establishes plastic read the article extrusion apart from other approaches.
Real-world Applications and Influences of Plastic Extrusion
In the world of manufacturing, the technique of plastic extrusion holds profound value. The financial advantage of plastic extrusion, primarily its high-volume and cost-efficient result, has actually reinvented manufacturing. The sector is constantly striving for technologies in naturally degradable and recyclable products, suggesting a future where the advantages of plastic extrusion can be retained without jeopardizing ecological sustainability.
Verdict
To conclude, plastic extrusion is a very efficient and effective technique of changing raw products right into varied products. It provides various benefits over various other plastic forming techniques, including cost-effectiveness, high output, marginal waste, and layout flexibility. Its effect is greatly felt in numerous sectors such as construction, auto, and consumer items, making it a crucial process in today's manufacturing landscape.
Digging deeper right into the technological process of plastic extrusion, it begins with the selection of the appropriate plastic product. Once cooled down, the plastic is cut into the called for lengths or wound onto reels if the product is a plastic movie or sheet - plastic extrusion. Comparing Plastic Extrusion to Various Other Plastic Forming Techniques
Recognizing the types of plastic suitable for extrusion leads the method for a more comprehensive conversation on how plastic extrusion piles up versus various other plastic developing approaches. Couple of other production processes can match the speed of plastic extrusion.
Report this page